The last 35 years in the supply chain management world were all about Lean Manufacturing, Just-In-Time, Kanban, and Zero Inventory. Somewhere along the way, as we continued looking for ways to cut costs, supply chains started to grow. As access to technology and information surged, we found that we could save money by out-sourcing to Asia and developing countries in other parts of the world. We also found countries with tax breaks and folded them into our supply chains. We became hyper-focused on saving money to grow profits. If we had to travel a little further for these savings, so be it.
I had a client whose manufacturing process of some of its products literally circumvented the planet. Manufacturing started in the US, was sent to the UK for further processing, then off to Singapore, and finally back to California. Long supply chains are a means that justify the ends, they rationalized.
But longer supply chains come with a cost, maybe not in the short term and maybe not directly, but anyone managing a supply chain in the last two years can tell you: long supply chains are unpredictable, precarious, and let’s face it, untenable.
And as supply chains get longer, so do lead times. And because of the long lead times, we are not able to respond to disruptions as quickly as we need to. The savings reaped by these practices are quickly offset and even exceeded by expedition costs, disruption in optimal production planning, and even lost sales.
As lead times get longer, inventories need to grow to cover the extended lead time. They also must grow to cover the growing uncertainty. Without a robust way to predict uncertainty, target inventories began to include a layer of emotional security. I had a client that spent an inordinate amount of time moving inventory around to make room for more. They even scrambled to add warehouses to hold the extra product. But this inventory gave them a sense of security, and so be it.
Inventory is an asset. Until it isn’t.
I’ve always questioned why inventory shows up on a balance sheet on the Assets side. I mean, it is an asset, until it isn’t. Too much inventory not only never gets used, which is an enormous waste of resources, but it covers up bad habits, poor quality, and broken processes. Another client had a fleet of tractor-trailers to house overflow, much of which was never used. They said to me once “If you want it, we don’t have it, and if we have it, you don’t want it.” That sounds a lot like a liability to me!
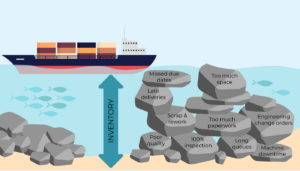
Reducing Waste: Increase Problem Visibility | Lower the Water to Expose the Rocks
Uncertainty will never go away; in fact, today it feels like it’s only getting worse – pandemics, military invasions, economic downturns, labor shortages, political dysfunction, and increasingly severe weather. Since there’s not much supply chain managers can do about these circumstances, there is another way to address the uncertainty besides more inventory: Shorten our supply chains.
Hedging for uncertainty is OK. Reducing uncertainty is better. We can’t stop the war in Ukraine; we can’t stop the extreme weather; and we can’t avoid the next pandemic or the next recession. But we can reduce the amount of uncertainty we have to deal with in our supply chains by shortening them.
Imagine if when a disruption occurs, you don’t have to wait three months for a new shipment from China. Imagine instead that your resources are nearby, and you could respond within 3 weeks.
Short supply chains mean lower lead time. Lower lead time means less inventory.
- In Transit – This type of inventory is completely useless. The sooner it gets to its destination, the sooner you can use it.
- Safety Stock – We hold safety stock to hedge against uncertainty. What’s one of the main inputs into safety stock calculations? Lead time.
- Cycle Stock – Cycles are shorter, so less inventory is needed to get you from one shipment to the next.
Short supply chains mean lower costs.
- You don’t need freight liners, a trove of international law experts, gobs of logistics planners, and massive warehouses to store everything.
- You will also incur fewer costs due to disruptions, including missed sales and expediting costs.
Short supply chains mean greater sustainability.
- All that inventory not getting made means less drain of our precious natural resources.
- Less distance traveled translates to fewer emissions.
- Supply chain management can be done efficiently and responsibly, not in a frantic panic mode.
Short supply chains mean greater circularity.
- By design, circular supply chains are short. When you aren’t starting from scratch, you save time and money. You don’t have to go to the mine, or the oil rig, or the forest. Instead, you are repairing, refurbishing, and repurposing.
Here at Arkieva, we have the tools to help you let go of some of that inventory in a way that ensures that you have what you need. We can help you compare a shorter version of your supply chain to the one you have now so that you can see the benefits clearly. Big or small, let us be your supply chain management partner.