One of the impacts of the recent rash of “upending events” such as COVID, shortage of products, severe weather activities, viral social media events that sink or spike demand, and “regular variability” is a recognition by many organizations that the critical requirement is responsiveness. This drives the need for scheduling and the dynamic interplay between scheduling and planning. Improving the scheduler’s world doesn’t start with advanced algorithms, but seven basic steps.
The scheduler has a difficult job because they must deal with many people who have conflicting objectives. The job is further complicated because the scheduler must gather a bunch of information from different sources. The scheduler spends most of the time gathering the right information, like the status of the shop floor, the demand in the next few weeks, the shutdown schedule, the projected receipts of raw materials, and so on. Well, the first task to improve the process is to make the job easier, by automating this data collection and providing the scheduler with a single window into all this data. Therefore, Step 1 in the scheduling application is to determine the data needed by the scheduler to do scheduling and gather it in one place.
The next problem that the scheduler has is that the data from many sources is not necessarily consistent. Besides, some of the data the scheduler needs is not kept in any system. Therefore, we need to provide the tools to analyze this data and point out inconsistencies. We need to identify problems like the schedule has an operation for 200 for a product, but you are swimming in inventory for that product. The scheduler has something scheduled, but there is no inventory of a component required for producing it, we are missing orders for product X, etc. Therefore, Step 2 in the scheduling application is to relate the data and determine internal consistency.
The other problem that you have is that even if the scheduler knows the problems, they can only react to the NEXT problem. It is difficult for you to see the consequences of the changes a scheduler makes without a tool to quickly show the consequences of changes. The scheduler may well be creating problems in the future, but you don’t know because there is no time to evaluate things well for a reasonable length of time. The best that you can do is worry about the next major event like a shutdown or demand spike. Therefore, in Step 3, the scheduling application provides an interactive environment that captures the scheduler’s decision(s), “simulates” the impact of the decision(s) to create a projected sequence of activities and creates a visual of the projected schedule. The direct benefit of this is that the scheduler will have a longer time horizon, the ability to see projected schedule, and an environment to try what-ifs.
If the consequences of the changes are going to be visible to the scheduler, we need to make sure that the changes are consistent with the business objectives as represented by the S&OP. Step 4 is to represent the S&OP plan within the scheduling environment and provide the tools to easily compare it with the current schedule.
The scheduler must deal with conflicting objectives from people in the organization. The marketing people always want to react to their needs, and meanwhile manufacturing are complaining about the schedule changes. To help the scheduler get some of these conflicts resolved, we’ll need to create a quantitative framework to measure how good a schedule is. Therefore, Step 5 is to create quantitative criteria for measuring the schedule. The objective is to quantify only those elements that can be supported with data. Of course, we can’t quantify everything, and it is not the intent to, but at least we can try to list the quantitative things like number of orders missed, setup costs, etc. to provide a way of costing out the schedule. The advantage of this is that the scheduler will be able to compare the quantitative attributes of two schedules. So now if marketing wants to make a change, the scheduler can calculate if it is going to cost 50,000 or 2,000. This will let the scheduler channel their energy to fight the important battles rather than fighting all of them.
If we do all the things above, we’ve just got to the point where we have some control over the scheduling. Once we are comfortable with this, the next thing is to reduce the repetitive work we do in maintaining the schedule. Therefore, Step 6 is to automate the routine activities in scheduling.
The steps up to now we haven’t really optimized anything and there may be much better ways of handling some of the tasks like lot sizing, and sequencing, and resource usage. Together with the scheduler, we can identify those opportunities, so Step 7 is to identify opportunities to optimize and implement these opportunities. This last step is an ongoing exercise and contributes to the sustainability of the solution
We can summarize these seven steps as:
- Determining and collecting the data needed
- Data consistency and gathering outside data
- Assessing, projecting, or making visible the consequences of a decision
- Is the decision consistent with the business objective
- Dealing with conflicting objectives
- Automate the routine aspects of scheduling
- Optimize – an ongoing exercise that contributes to the sustainability of solution
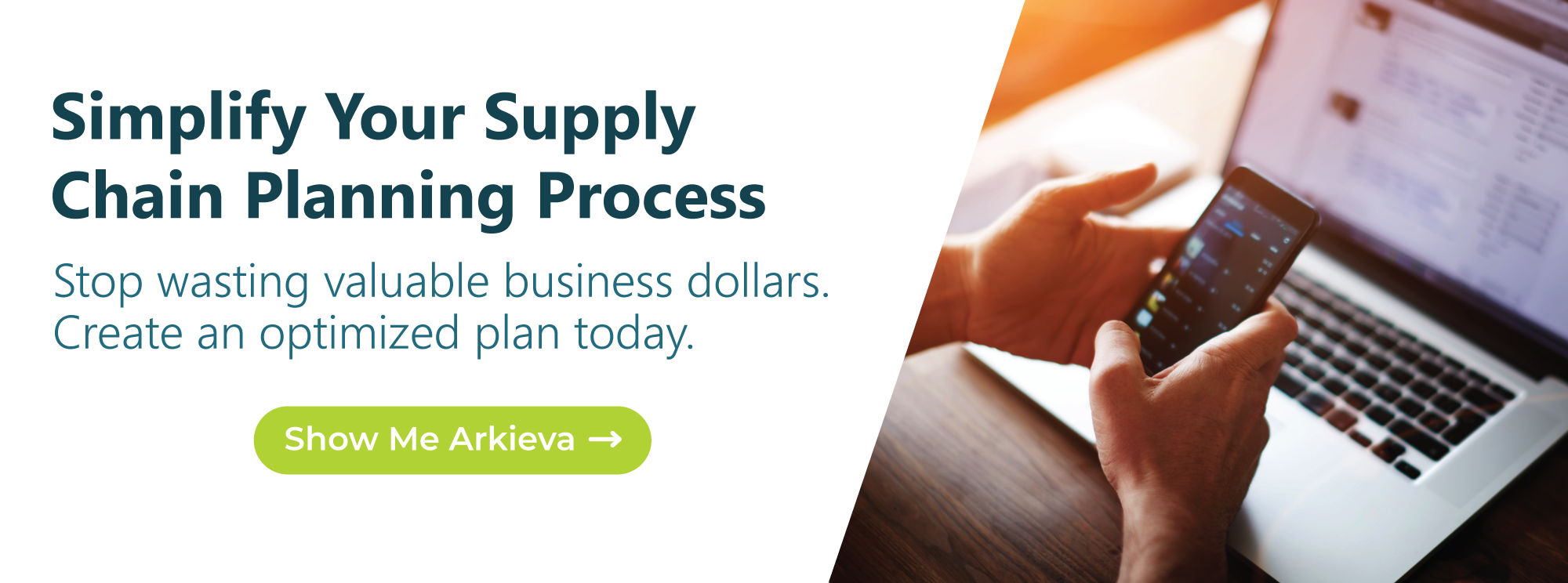
About the Author: Venkat Nagasubramanian
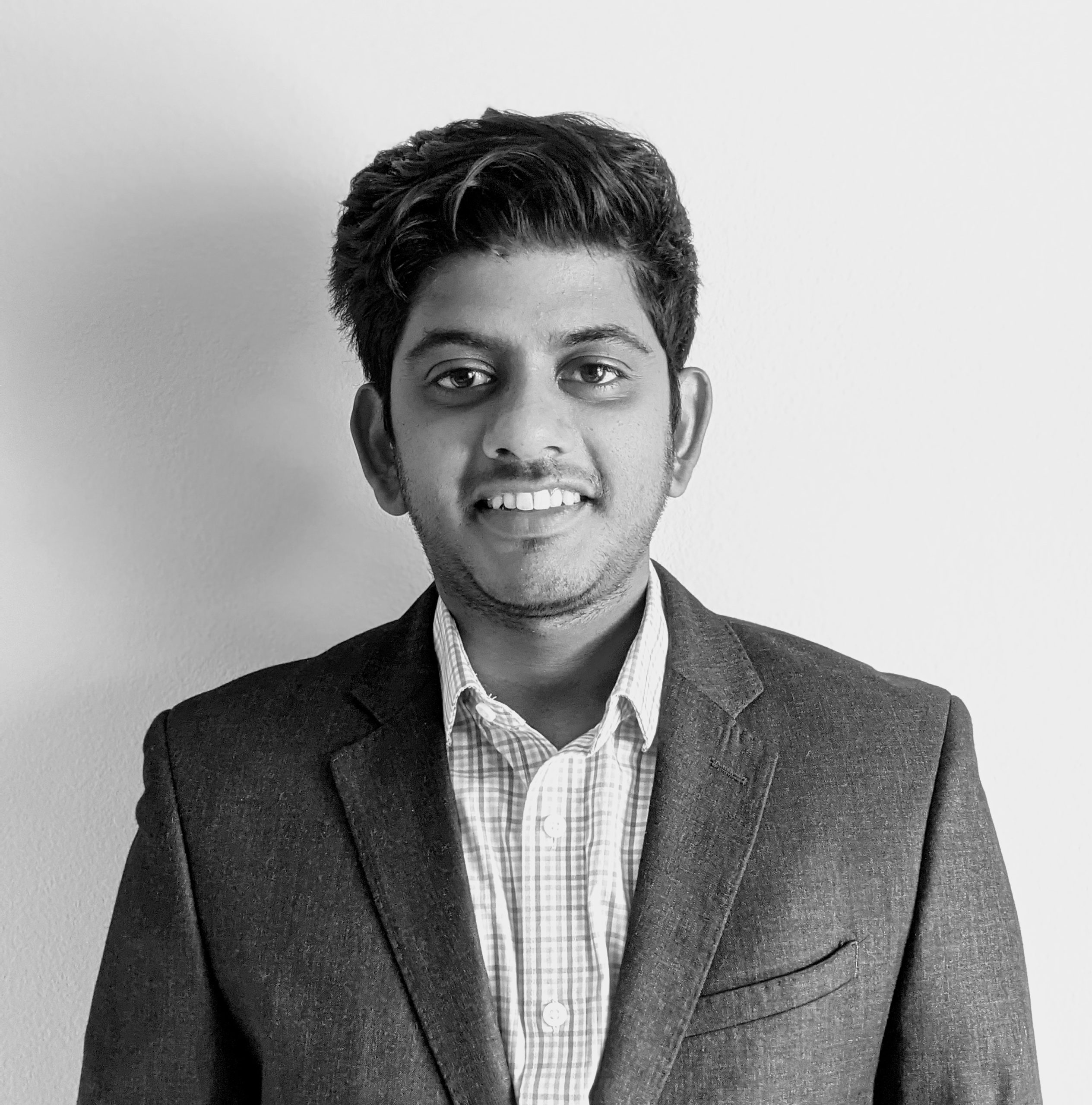
Venkat Nagasubramanian, currently serving as an Optimization Expert in Pre-Sales, brings a wealth of experience from his consulting background where he led the implementation of decision support systems and optimization models. With a master’s degree in industrial engineering, Venkat excels in the realm of supply chain optimization, demonstrating both analytical acumen and strategic insight. Outside of his professional commitments, he is an enthusiastic biker and soccer lover, reflecting a comprehensive dedication to excellence in various aspects of his life.