From talks of an autonomous supply chain, a robotic takeover, drone deliveries in 30 minutes or less; the future of supply chain management presents businesses with the opportunity to transform their processes into a competitive advantage.
While it is nice to envision supply chains in 2020 or 2030 the truth is; for many manufacturing businesses, discussions about future supply chain innovations, often leads to a “yeah..right,” smirk by supply chain executives – this with good reason.
Most manufacturing businesses still, face day-to-day supply chain optimization issues that span from having manual processes to having difficulties in syncing up projected sales with actual market conditions. For such businesses, they need to walk before they run. Taking advantage of more advanced supply chain innovations comes only after essential planning, automation, and optimization processes have been put in place.
The first step towards an optimized supply chain starts with a supply chain assessment. This looks at all the businesses’ current manufacturing and supply chain processes. The goal of the evaluation is to identify waste areas, specifically, ways that current processes can be enhanced to reduce costs and improve delivery times.
Related: How to Perform a Supply Chain Management Assessment for 2017
3 Key Supply Chain Initiatives That Can Help Manufacturing Businesses Today
1. Improving Forecast Accuracy
Demand planning is a critical component in any supply chain planning process. Forecasts drive most downstream supply chain processes because they help supply chain leaders determine the amount of raw materials needed; and how to gauge inventory levels to avoid overstocks or an understock. For companies struggling with forecast accuracy, high inventory costs may leave no room for additional cost savings that could be invested in supply chain innovation projects.
2. Data Cleansing and System Integration
Data Cleansing and System Integration should be a key initiative for any business looking to improve forecasted numbers, enhance collaboration, and supply chain visibility. Inaccurate forecasting often stems from inaccessibility to real-time data. Using manual Excel spreadsheets for planning and forecasting can lead to forecasting errors and even disastrous Excel errors. Integrating your ERP with advanced planning systems can eliminate error-prone manual steps, and improve team productivity with access to real-time transactional data on the fly. For businesses with disjointed back office and planning systems, improving forecast accuracy maybe rather elusive.
3. Determine the Metrics That Matter
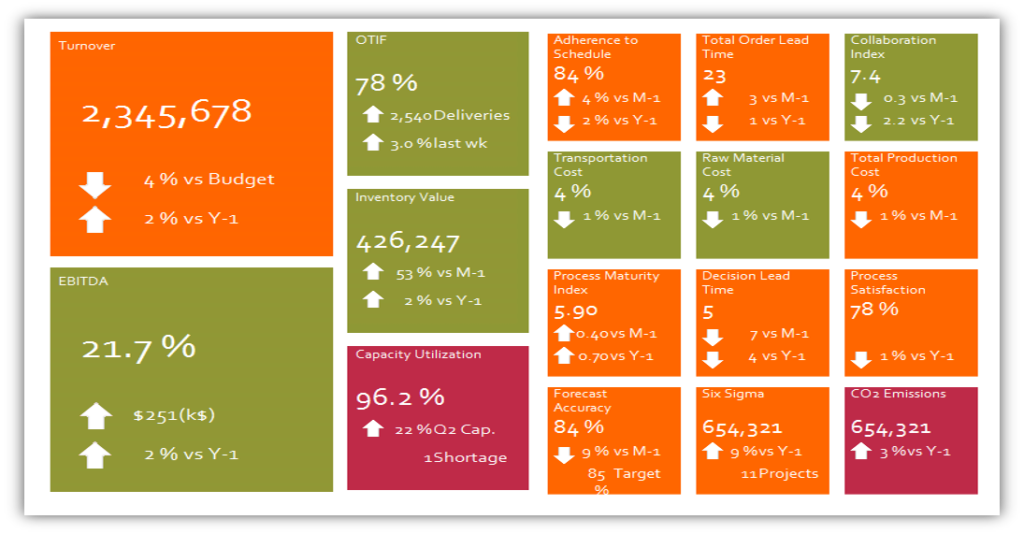
Source: Arkieva
Read Also: 7 Supply Chain Technology Trends Set to Disrupt Supply Chains in 2017 and Beyond
Determining the metrics that matter goes beyond just implementing a ‘pretty’ S&OP dashboard that identifies leading indicators to help drive the business forward. These key metrics should allow supply chain managers to easily and quickly identify critical gaps in the supply chain process. Examples of key metrics include capacity utilization, forecast accuracy, lead times, and turnover rates.
All in all, businesses should not begin to create supply chain strategies that could be advantageous for 2020 and beyond, without looking at ways to improve what exists today. Remember, any technological enhancement is only as good as its implementation. Unfortunately for most manufacturing businesses with subpar supply chain processes, implementing more advanced supply chain solutions might be a far reach, involving jumping critical steps essential to attaining true supply chain visibility and process optimization.